Three Key Benefits of Using Non-Spill Quick Couplings
Posted by Fluid Gas Handling Team on 12 Dec 2018
Quick couplings allow fluid lines to be quickly and easily connected and disconnected without the need for tools. Non-spill or dry break couplings are a specific type of connector designed to eliminate spillage during a connection and disconnection.
What sets non-spill apart from traditional couplings? The flush face valve is the difference maker as this feature minimizes discharge and trapped air, while ensuring repeated dripless connections and disconnections. Non-spill or dry break quick disconnects are key to maintaining a clean environment, protecting system fluids from contamination caused by air or debris, and most importantly, keeping workers safe.
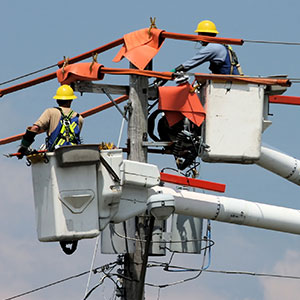
Environmental protection
Did you know 98 million gallons of fluid from hydraulic equipment is improperly deposited into topsoil, groundwater, rivers and lakes annually? That’s according to the National Oceanic and Atmospheric Administration (NOAA). The statistics are staggering when you come to the realization that one liter of oil can pollute up to one million liters of water.
Fluid leaks and spills have the potential to cause significant environmental issues. If contamination were to occur, organizations would be responsible for damage to ecosystems and wildlife, resulting in high cleanup costs and federal penalties. All industries from agricultural food production to manufacturing and service operations are affected by environmental protection regulations.
Even what looks like a small leakage can sometimes leave lasting effects on our precious planet. Non-spill quick disconnects keep fluids contained and its environmental impact to a minimum. The flush face valve quickly shuts off flow when fluid lines are disconnected and is engineered to eliminate spillage and fluid loss.
Maintain system performance
Hydraulic equipment relies on fluid system integrity to effectively transmit power for instant, accurate response and reliable performance. Contamination and the loss of performance transpire when debris and air work their way into the hydraulic fluid. It’s common for this to occur when dirt accumulates on the exposed surface of a traditional poppet valve tip when disconnected. Then, when the quick coupling is reconnected, air and contamination are pushed into the system fluid as the poppet valves open. The air and contamination can cause a loss of horsepower, temperate performance abnormalities and a variety of detrimental effects.
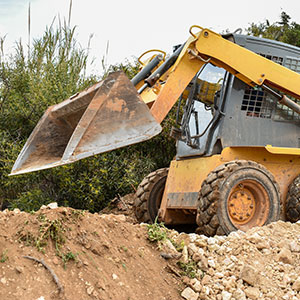
The flush face valves of non-spill quick couplings do not provide surfaces or areas for dirt to accumulate and collect. In environments where dirt is present, the smooth flat surface of the coupling end can be easily and quickly wiped clean. Additionally, non-spill valves keep air inclusion to a minimum because the flat-faced surface does not trap pockets of air as fluid lines are reconnected.
Promote workplace safety
There are many safety and ergonomic risks associated with hydraulic system leakage. Exposure to dangerous chemicals and confined spaces significantly enhance the chances of injury during maintenance operations. Slips, trips and falls account for a third of all personal injuries and is a top cause of workers’ compensation claims.
The most common reason why? Wet or oil surfaces as a result of incremental leakage. Spills and leaks can happen at any point and pose a wide range of health hazards to workers such as sensitization and irritation as well as physical risks.
Parker’s non-spill quick couplings
Parker offers a variety of non-spill couplers to fit versatile fluid applications. The FEM Series and 71 Series are both ideal for use in applications where air inclusion and fluid loss must be minimal. When chemical compatibility is also needed, Parker’s FS Series is a good option.
Three Key Benefits of Using Non-Spill Quick Couplings Non Spill Couplings Parker’s FEM Series is compliant with the highest design and performance specifications set forth by ISO 16028. The standard defines a common dimensional and performance profile that ensures global compatibility and interchangeable connectability with other manufacturer’s quick couplings built to the same standard. Parker’s FEC Series nipples also provide the ability to connect under trapped residual system pressure. FEM Series quick couplings are constructed from steel material and are commonly used to connect hydraulic lines to tools used in construction and utility work. In addition, they are widely used on skid loaders and other similar machinery.
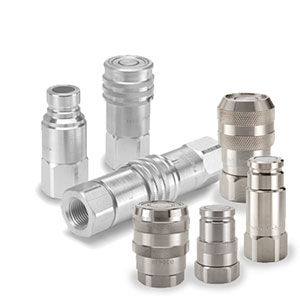
The 71 Series, an original Snap-tite design non-spill coupling, is rated for working pressures up to 10,000 psi. With material options featuring steel, 316 stainless and high pressure stainless steel, Parker’s 71 Series non-spill quick couplings are utilized in industrial applications as well as topside offshore oil drilling and construction.
FS Series non-spill quick couplings provide excellent chemical compatibility. The all stainless steel construction and Fluorocarbon seals make them ideal for closed system transfer of chemicals or corrosive media. Other applications include food processing and chemical dispensing.
The FEM Series | 71 Series | FS Series couplings are available for purchase on Parker.com. Simply add products to your cart for shipment within two days for in-stock items.
|